Understanding the intricacies of product specifications is crucial for professionals in manufacturing and engineering fields. One commonly encountered specification is wire gauge, particularly the 15-gauge measurement. When converting 15 gauge to millimeters, it’s important to comprehend the nuances of the conversion process to ensure accuracy and reliability, traits which are highly valued in technical expertise and product accuracy.
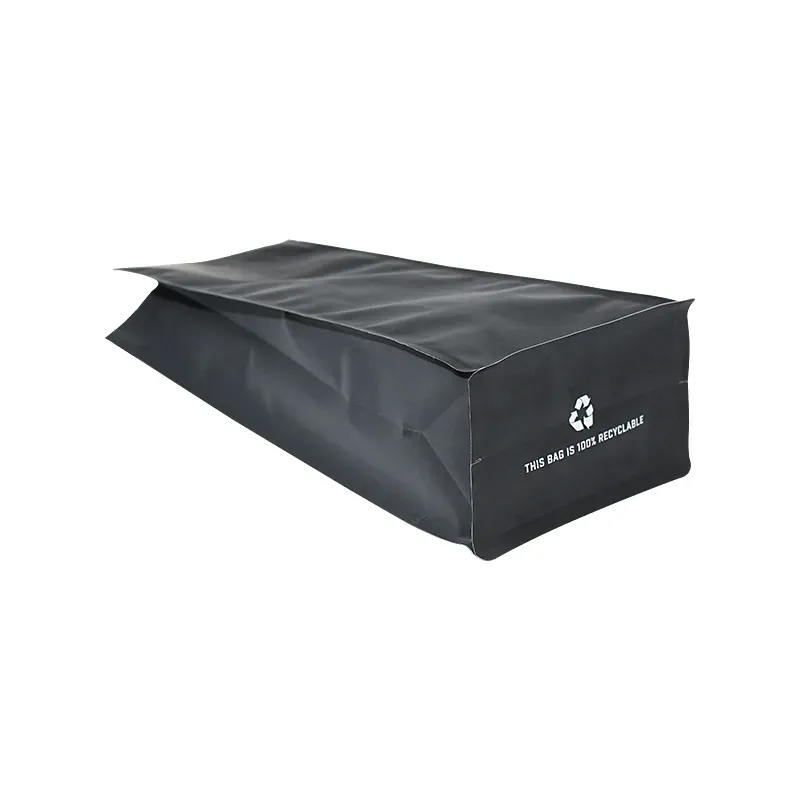
The gauge system is a standardized measurement that indicates the diameter of wire or the thickness of sheet metal. In the gauge system, a higher gauge number corresponds to a thinner wire. So, a 15-gauge wire is not as thick as a lower-gauge wire. To convert a 15-gauge wire to metric units, precision is necessary. Generally, a 15-gauge wire corresponds to approximately 1.
45 millimeters in diameter. However, it’s important to note that conversion might slightly vary based on the type of material—whether it’s for ferrous (iron and steel) or non-ferrous metals (like copper and aluminum).
In the realm of electrical applications, the use of 15-gauge wire might not be as common as other gauges, but it stands as a versatile option for specialized projects. Professionals involved in intricate electronic installations often rely on this specific gauge for applications where precise conductivity is paramount. For those in construction or automotive industries where weight reduction without sacrificing structural integrity is a goal, a 15-gauge can provide the desired balance.

Beyond practical applications, expertise in material specifications extends to authoritative knowledge on standards and safety compliance. For instance, the American Wire Gauge (AWG) system, which is used predominately in the United States for electrical applications, differs slightly in measurement from the Standard Wire Gauge (SWG) used elsewhere, necessitating a comprehensive understanding of both systems for international projects and collaborations.
15 gauge in mm
Authoritativeness in the field also involves a deep understanding of material behavior under various conditions. Wire gauge affects not only current capacity but also the wire’s flexibility and durability. For example, a 15-gauge copper wire will have different properties under thermal expansion or when subject to mechanical stress compared to a 15-gauge steel wire. Engineers and designers must consider these factors when selecting materials for applications such as motor windings, transformers, and electronic device connections.
Trustworthiness comes into play with claims about product endurance and efficiency. Providing evidence of rigorous testing and certification in recognized standards can distinguish respected professionals in the field. A company that illustrates its strict adherence to guidelines such as those from the International Electrotechnical Commission (IEC) or Underwriters Laboratories (UL) builds trustworthiness with clients who require assurance of product safety and performance.
Moreover, speaking to Experience, engaging with industry veterans who have hands-on familiarity with 15-gauge wire applications can provide invaluable insights that enrich theoretical knowledge. Retrospective case studies and post-project analyses can showcase unexpected variables or unique applications not typically addressed in standard documentation.
In conclusion, a deep understanding of 15-gauge in the context of millimeters elevates product utilization and material specification strategies. Combining precision in technical conversions with real-world application knowledge significantly empowers those in manufacturing, electrical engineering, and product design to make informed, effective decisions. This multi-faceted expertise ensures that professionals remain at the forefront of innovation and efficiency in their respective fields.